To ensure safety and extend battery life, follow these guidelines:
1. Environment: Store in a dry, cool, and well-ventilated place. Avoid direct sunlight and heat sources. Recommended temperature: 5°C–25°C; humidity: 45%–75%.
2. Charge level:
-Lead-acid: Fully charge before storage; recharge every 3 months.
-Lithium: Store at 30%–60% charge; check voltage every 6 months and recharge if needed.
3. Safety: Prevent short circuits by insulating terminals. Keep away from metal objects. Avoid drops and strong impacts.
4. Separation: Clearly label and separate new and used batteries. Recycle used batteries promptly.
5. Packaging: Use original or insulated packaging to protect from dust, moisture, and physical damage.
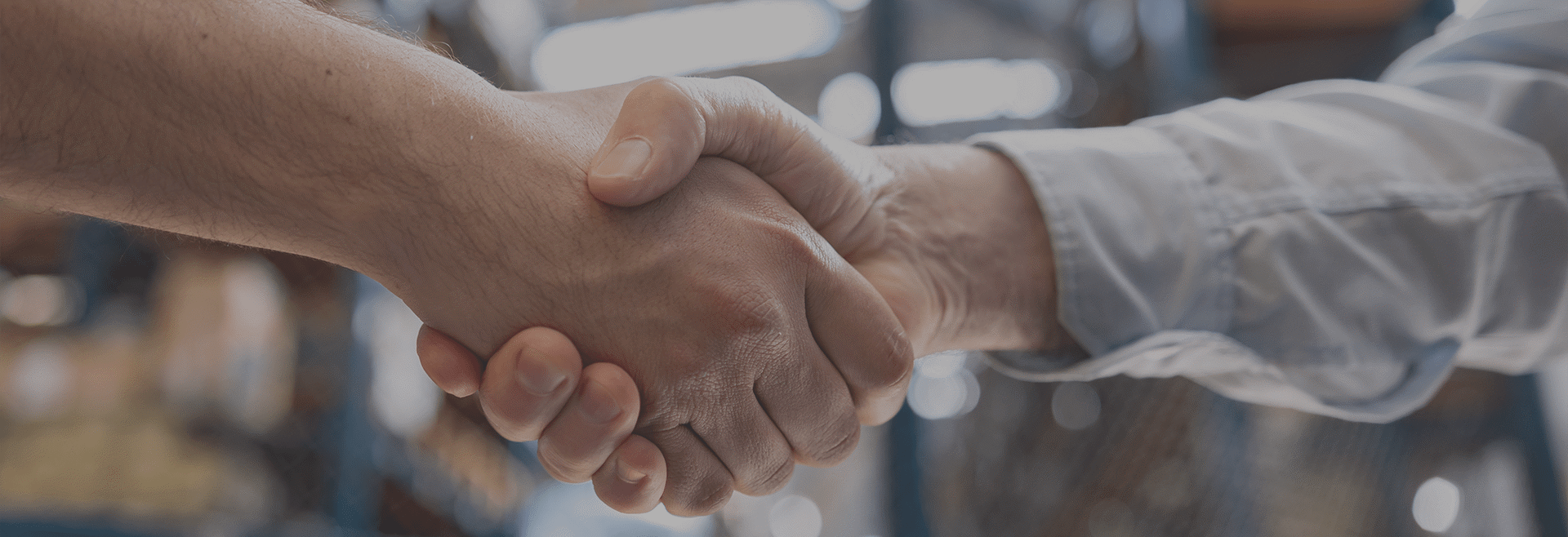
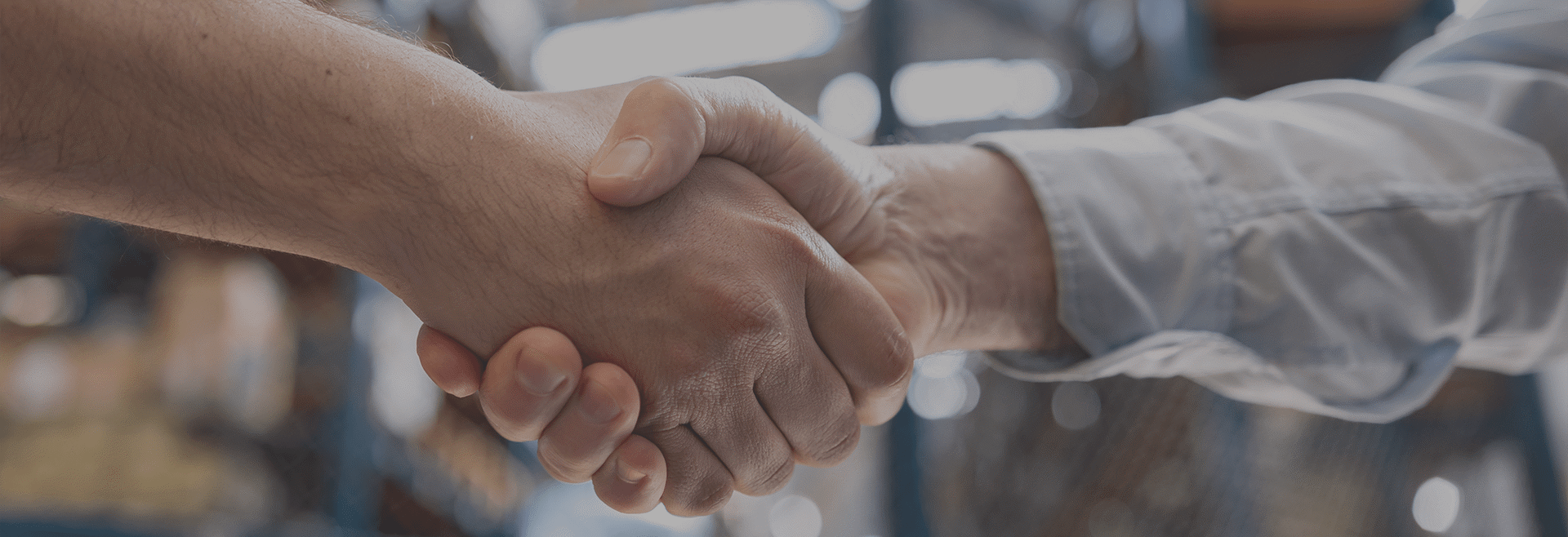
Support
Robust service system ensuring reliable customer support.
Support
FAQs
FAQs
For questions, check the FAQ below. Need more help? Contact us for a tailored solution.
Service Hours: Mon–Fri, 9:00–18:00 (Beijing Time)
Email: info@vision-batt.com
Service Hours: Mon–Fri, 9:00–18:00 (Beijing Time)
Email: info@vision-batt.com
01Common Questions
-
qHow to properly store batteries?a
-
qHow to apply for after-sales service?aYou can apply for after-sales service through any of the following methods:
1. Online Application: Visit the "After-Sales Service" page on our official website, fill in the product details and issue description. Our customer service will contact you within 1 working day.
2. Email Application: Send an email to [sales@vision-batt.com](mailto:sales@vision-batt.com) with the product model, fault description, and your contact information.
To speed up processing, please provide as much of the following information as possible: product model, purchase date, fault symptoms, on-site photos or videos (if any). We will arrange service according to the warranty policy. -
qWhat should be noted when transporting batteries?aEnsure batteries pass UN38.3 testing before shipment, use shockproof and short-circuit-proof packaging with proper labeling. Lithium batteries for air transport must not exceed 30% charge and require complete transport documentation. Damaged or swollen batteries are prohibited from transport.
02Lead-acid Battery
-
qWhy is there white residue around the battery vent? Is it leaking?aThis is usually not a leak, but a normal reaction. During charging, a small amount of gas may escape through the vent, carrying acid mist. When it reacts with dust or alkaline substances in the air, it forms white salt-like crystals.
You can gently wipe it off with a clean cloth. Wear insulated gloves and safety goggles when cleaning. This does not affect battery performance.
To prevent it:
1. Keep the battery area dry and clean
2. Avoid humid, dusty, or corrosive environments
3. Do not block the vent holes—ensure gases can escape freely
-
qWhat causes battery swelling (bulging)?a1. Incorrect charging settings or faulty charger output can cause overcharging, high current, or long charging time. This leads to gas buildup inside the battery, increasing internal pressure and causing swelling.
2. Poor heat dissipation due to tight installation or high-temperature environments can speed up chemical reactions and raise internal pressure.
3. Blocked ventilation or covering the battery with other objects can trap heat during charging or use, leading to swelling.
What to do:
Follow the battery manual to set correct charging time and voltage. Check that the charger’s output current is normal. Avoid both overcharging and undercharging. For detailed charging and installation guidelines, refer to the product manual.
-
qWhat should I do if a lead-acid battery is leaking?aIf you notice liquid leakage or a strong smell during use, it may be caused by a cracked case, poor sealing, or overcharging that leads to high internal pressure. Strong shocks or impacts during transport or use can also damage the case and cause leaks.
Check the battery carefully:
-If it's a manufacturing defect (e.g. poor sealing), we recommend replacing the battery.
-If there are signs of physical damage (e.g. cracks), replace the battery immediately. -
qWhat causes a battery to have a short lifespan?aIf a battery doesn’t last as long as expected — for example, it’s supposed to work for 2–3 years but shows problems within a year — the reasons may include:
1. Poor battery quality (e.g. bad materials or production issues)
2. Improper use (e.g. frequent over-discharge, incorrect charging, or use in extreme temperatures)
We suggest trying an equalization charge and retesting. If the problem continues, return the battery for further analysis. (See the product manual for equalization charging instructions.)
03Lithium Battery
-
qWhy won't the battery power on?aIf there's no relay click sound and the BMS doesn't start after holding the power button for 3 seconds, follow these steps to check:
1. Check relay wiring
Make sure the self-locking relay is wired correctly, with no loose or reversed connections.
2. Check BMS power input
Use a multimeter to see if the BMS input terminal has normal voltage.
3. Check the power button indicator
If there’s no response after holding the button for 3 seconds and the light goes off shortly after, the battery failed to power on.
4. Use a CAN box for diagnosis
Connect a CAN box to the battery's debug port. While holding the power button, use the upper computer to check battery status, BMS fault codes, and workflow for further analysis. -
qWhy can't the battery be charged?aIf the battery can't be charged using the designated charger, follow these steps to troubleshoot:
1. Check charger compatibility
Make sure you’re using the original or recommended charger that matches the battery model.
2. Check battery voltage
Use a multimeter to measure total voltage. If the battery is over-discharged (below the startup voltage), it won't power on even after pressing the switch. Try boosting it briefly with a DC power supply or a lead-acid charger before regular charging.
3. Check charger output
Verify the charger outputs 12V to ensure it’s working properly.
4. Check communication data
Use a CAN box to capture communication between the charger and battery to see if there are any issues.
5. Check communication interface wiring
If the battery doesn’t respond after plugging in the charger and there are communication errors, the connectors may be reversed. Check that communication lines on both the vehicle and battery sides are correctly connected. -
qWhy is the LiFePO₄ battery not heating?aIf the ambient temperature meets the heating conditions (for charge or discharge heating) but the system doesn’t start heating, follow these steps to check:
1. Check the heating circuit resistance
Enter “Relay Force Control” mode via the upper computer:
-Disconnect Relays 1, 2, and 6
-Connect Relays 4 and 5
2. Measure resistance with a multimeter
-Between P+ and Series + (Box A)
-Between Series − and P− (Box B)
Normal range: 2.0-3.0Ω.
If no resistance is detected, open the box to inspect the internal circuit.
3. Check the heating relays
After forced relay closure, check if the relay terminals in Box A and B are conducting. If not, replace the relay.
4. Check the heating cable
Make sure all cable connections are secure. Use a multimeter to check continuity from end to end. If not conductive, check each connection point.
04UPS
-
qWhat causes communication, voltage, or temperature self-check failure?aPossible Causes:
1. Wiring issues
2. Incorrect DIP switch settings
3. Poor network cable connection
Solutions:
1. Check the network cable between CBMS and GBMS to rule out cable or hardware faults. If the LCD shows CBMS communication error, it’s often due to incorrect wiring between CBMS and GBMS.
2. Verify the DIP switch settings for the parallel CBMS IP address, and ensure CAN/485 termination resistors are enabled on GBMS and the last battery cabinet’s CBMS.
3. Inspect network cable connections between units for poor contact or loose connections. -
qWhy can't the battery be charged?aPossible Causes:
1. Charger or UPS mainboard failure
2. Battery over-discharge triggered protection (voltage below cutoff level)
3. BMS (Battery Management System) malfunction
Solutions:
1. Check if the charger output matches the battery specifications
2. Try activating the battery using professional equipment
3. Contact after-sales service to check the BMS or replace the battery -
qWhy is the battery runtime short or capacity dropping fast?a1. Possible Causes
-Long-term overcharging or over-discharging leads to battery aging
-Extreme temperatures affect performance
-Battery cycles are nearing the designed lifespan
2. Usage Tips
-Avoid deep discharges to extend battery life
-Keep the working temperature around 25℃ ± 5℃
3. Next Steps
If the capacity drops significantly, contact the manufacturer for professional inspection and maintenance.